An Australian EV charger and battery maker is not deterred by this year’s spectacular failure of Brisbane producer Tritium when it starts local production in October in southeast Queensland.
eLumina has showed off its new manufacturing centre at Yatala where it will employ 300 staff to build EV chargers and community batteries. Initial output will be 300 units per year at the $20m, 2500 sqm facility.
Once valued at $2bn, Tritium planned to install more than 300 of its EV fast chargers nationwide and had gained traction in the global EV fast charging market. However, it crashed and left behind a network of EV chargers across Australia that no longer can be serviced and need to be replaced. It was placed into voluntary administration in April.
eLumina is not only out to show it will succeed where Tritium failed. It’s moving its manufacturing operation from Shanghai to Yatala as questions persist about the competitiveness of Australian produced products in the renewables space.
CEO Lisa Marsh is adamant that eLumina’s operation is different. First, it is a battery maker as well as fast charger manufacturer and Tritium wasn’t. Combining a battery and fast charger allowed its large D1 DC fast chargers to be installed anywhere in the country, whether there was local power available or not.
Second, it was using standard locally produced parts for its units. Tritium in contrast had relied on specially designed parts whose lack of availability led to supply chain issues.
Third, eLumina has managed to survive with private sector funding.
Fourth, eLumina is increasing manufacturing at a time when demand for EVs and charging is building.
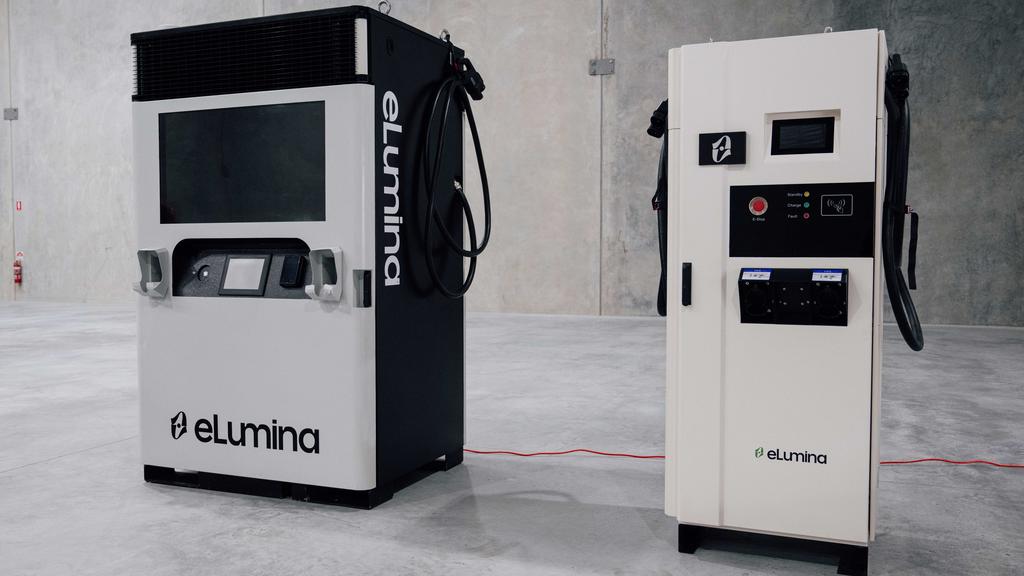
Ms Marsh said the company would upscale to a 15,000 sqm facility with a 1000 unit annual rollout within three years.
Some organisations are replacing Tritium chargers with eLumina D2 chargers which are technically comparable.
Ms Marsh said its combined battery/charger D1 DC fast chargers surpassed what had been available in Australia before. D1 units could draw on solar energy, stable and unstable power sources to deliver a 204kW output from just a 40kW input. The units were rugged and could be placed anywhere irrespective of available local power.
eLumina will provide charging capabilities to bus and truck depots, supermarket distribution centres and commercial hubs.
Ms Marsh said eLumina would produce “mid capacity” community batteries at the Yatala factory. Their main use would be powering schools, hospitals, police stations, large farms, supermarket centres, data centres and other public utilities, and replacing installations that use diesel generators as a back-up solution.
However, Australia’s fledgling manufacturing sector faces competition from China which can produce cheaper components. China also dominates the processing of the minerals needed for batteries and clean energy.
Ms Marsh is among the industry figures that do not advocate imposing tariffs on China’s batteries and chargers, at least initially. They say tariffs would ramp up the cost of renewable components in the early stages of adoption. Tariffs were a different proposition later.
“I definitely don’t think (tariffs) initially,” Ms Marsh said. “I think while they may be producing batteries, there’s still issues with the supply chain, and parts and things like that. And having everything local does speed up the supply chain.”
She said eLumina was maintaining its relationship with China’s CATL which supplied the battery cells.
Local industrial laser cutting firm GCI Group will provide galvanised shells for battery units.
eLumina was also partnering with Addelec, an installer of EV charging stations with national asset management capabilities.
She said locally made batteries and chargers were a better proposition for Australia.
“Our batteries are designed for the Australian climate. We have liquid cooling and we have galvanised shells. We’ve taken into consideration the landscape because they’ll be outdoors, and we can put them anywhere.”
The D1 EV system will retail at $250,000 ex GST. Community batteries were available with 200, 1000, and 1500kWh capacity and cost from $160,000 upwards.
The factory has the backing of Gold Coast City Council. Mayor Tom Tait said the Gold Coast wanted to secure a large slice of the clean energy sector and the skilled jobs it created.